Начар суу каршылык, тегиз эмес бети, жогорку порошок мазмуну жана бирдей эмес узундугу? Суу тоют өндүрүүдө жалпы көйгөйлөр жана жакшыртуу чаралары
Суу тоюттарынын күнүмдүк өндүрүшүндө биз ар кандай аспектилерден айрым көйгөйлөргө туш болдук. Бул жерде ар бир адам менен талкуулоо үчүн кээ бир мисалдар бар:
1、 Формула
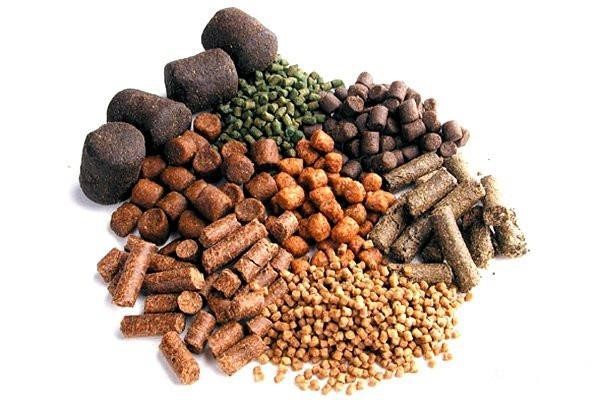
1. Балык азыгынын формулалык структурасында чийки булага кирген рапс унун, пахта унун ж.б.у.с. Кээ бир мунай заводдору алдыңкы технологияга ээ жана май негизинен кургак куурулган, мазмуну өтө аз. Анын үстүнө чийки заттын бул түрлөрү өндүрүштө оңой сиңбейт, бул грануляцияга көп таасирин тийгизет. Мындан тышкары, пахта унун натыйжалуулугун таасир этет, майдалоо кыйын.
2. Чечим: Рапс тортунун колдонулушу көбөйүп, формулага күрүч кебеги сыяктуу жогорку сапаттагы жергиликтүү ингредиенттер кошулду. Мындан тышкары, формуланын болжол менен 5-8% түзгөн буудай кошулган. Жөнгө салуу аркылуу 2009-жылы грануляциялык эффект салыштырмалуу идеалдуу болуп, тоннадан түшүмдүүлүк да жогорулаган. 2,5 мм бөлүкчөлөр 8-9 тоннанын ортосунда болуп, мурункуга салыштырмалуу дээрлик 2 тоннага көбөйгөн. бөлүкчөлөрдүн көрүнүшү да бир топ жакшырды.
Мындан тышкары, пахта унун майдалоонун эффективдуулугун жогорулатуу учун биз пахтанын унун жана рапстын унун майдалоонун алдында 2:1 про-порциясында аралаштырдык. Жакшыртылгандан кийин, майдалоо ылдамдыгы рапс унун майдалоо ылдамдыгы менен бирдей болду.
2、 Бөлүкчөлөрдүн тегиз эмес бети
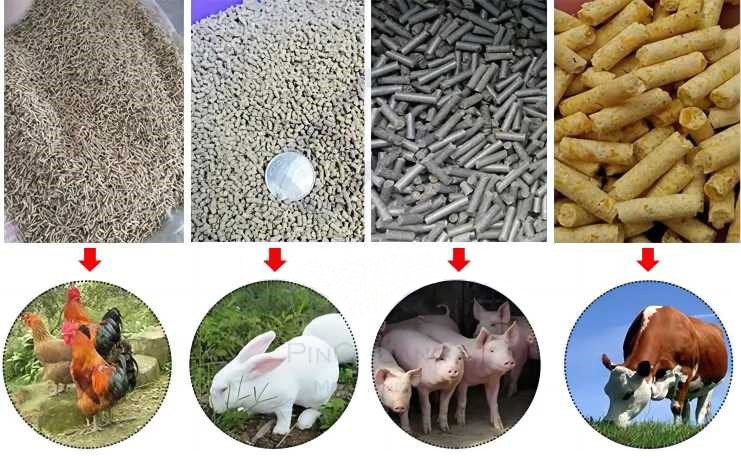
1. Даяр продукциянын сырткы көрүнүшүнө чоң таасирин тийгизет, сууга кошулганда кулап түшүүгө жакын жана пайдалануу көрсөткүчү төмөн. негизги себеби болуп саналат:
(1) чийки заттар өтө орой майдаланган, жана чыңдоо учурунда, алар толук жетилген жана жумшартылган эмес, ошондой эле калыптын тешиктеринен өтүп жатканда башка чийки заттар менен айкалыштыруу мүмкүн эмес.
(2) чийки була жогорку мазмуну менен балык тоют формулада чийки затта буу көбүкчөлөрүнүн болушуна байланыштуу, чыңдоо процессинде, бул көбүкчөлөр бөлүкчөлөрдү кысуу учурунда калыптын ичиндеги жана сыртындагы басымдын айырмасынан улам жарылып, бөлүкчөлөрдүн тегиз эмес бетине алып келет.
2. Иштөө чаралары:
(1) Майдалоо процессин туура көзөмөлдөө
Азыркы учурда, балык тоют өндүрүүдө, биздин компания жапырт чийки зат катары 1,2 мм электен микро порошок колдонот. Биз майдалоонун тактыгын камсыз кылуу үчүн электин колдонулуш жыштыгын жана балканын эскирүү даражасын көзөмөлдөйбүз.
(2) буу басымын көзөмөлдөө
Формула боюнча, өндүрүш учурунда буу басымын жөндөп, жалпысынан 0,2 тегерегин көзөмөлдөңүз. Балык азыгынын формуласында ири була чийки заттын көп болушуна байланыштуу, жогорку сапаттагы буу жана акылга сыярлык температура талап кылынат.
3、 Бөлүкчөлөрдүн сууга туруктуулугу начар
1. Көйгөйдүн бул түрү биздин күнүмдүк өндүрүшүбүздө эң кеңири таралган, көбүнчө төмөнкү факторлор менен байланышкан:
(1) Кыска убакыт жана төмөн температура бир калыпта эмес же жетишсиз муздатуу, төмөн бышкан даражасы жана жетишсиз нымдуулук алып келет.
(2) Крахмал сыяктуу жабышчаак материалдар жетишсиз.
(3) шакек көктүн кысуу катышы өтө төмөн.
(4) мунай мазмуну жана формула чийки була чийки заттын үлүшү өтө жогору.
(5) Майдалоочу бөлүкчөлөрдүн өлчөмү фактору.
2. Иштөө чаралары:
(1) буу сапатын жакшыртуу, жөнгө салуучу бычак бурчун тууралоо, чымыркануу убактысын узартуу жана тиешелүү чийки заттын нымдуулугун жогорулатуу.
(2) Формуланы тууралаңыз, крахмал чийки затын тийиштүү түрдө көбөйтүңүз жана майдын жана чийки була чийки затынын үлүшүн азайтыңыз.
(3) Зарыл болсо, чаптама кошуңуз. (Натрий негизиндеги бентонит шламы)
(4) кысуу катышын жакшыртуушакек өлөт
(5) Кудуктун майдалоонун майдалыгын көзөмөлдөө
4、 бөлүкчөлөрүндө ашыкча порошок мазмуну
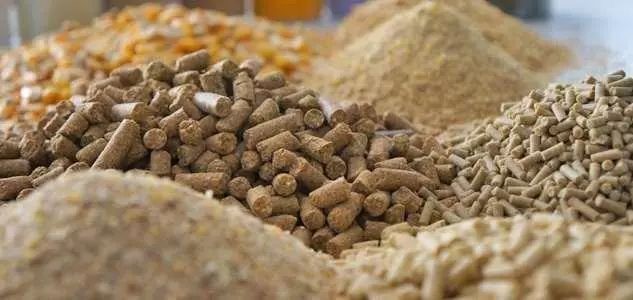
1. Муздаткандан кийин жана сүзүү алдында жалпы гранул тоюттун көрүнүшүн камсыз кылуу кыйын. Кардарлар гранулдарда майда күл жана порошок көбүрөөк экенин айтышкан. Жогорудагы анализдин негизинде, мен мунун бир нече себептери бар деп ойлойм:
A. бөлүкчөлөрдүн бети жылмакай эмес, кесүү тыкан эмес, бөлүкчөлөр бош жана порошок өндүрүүгө жакын;
B. Экранды баалоо боюнча толук эмес скрининг, тыгылып калган экран торлору, резина топторунун катуу эскириши, экрандын торунун апертурасы туура келбегендик, ж.б.;
C. Даяр продукт кампасында майда күл калдыктары көп, жана жол-жоболоштуруу кылдат эмес;
D. Таңгактоо жана таразага тартуу учурунда чаңды тазалоодо жашыруун коркунучтар бар;
Колдоо чаралары:
A. Формула түзүмүн оптималдаштыруу, шакек өлчөгүн акылга сыярлык тандоо жана кысуу катышын жакшы көзөмөлдөө.
B. гранулдоо жараянында, чийки зат толугу менен бышып жана жумшартуу үчүн чыңдоо убактысын, азыктандыруу өлчөмүн жана гранулдаштыруу температурасын көзөмөлдөө.
C. Бөлүкчөлөрдүн кесилишинин тыкан болушун текшериңиз жана болот тилкеден жасалган жумшак кесүүчү бычакты колдонуңуз.
D. Баалоо экранын тууралаңыз жана сактаңыз жана акылга сыярлык экран конфигурациясын колдонуңуз.
E. даяр продукт кампасынын астында орто скрининг технологиясын колдонуу абдан порошок мазмуну катышын азайтууга болот.
F. Даяр продукциянын кампасын жана схемасын өз убагында тазалоо зарыл. Мындан тышкары таңгактоо жана чаңдан тазалоочу аппаратты жакшыртуу зарыл. Чаңды тазалоо үчүн терс басымды колдонуу эң жакшы, бул идеалдуураак. Өзгөчө таңгактоо процессинде таңгактоочу жумушчу таңгак шкаласынын буфердик буфериндеги чаңды дайыма тыкылдатып, тазалап турушу керек..
5, Бөлүкчөлөрдүн узундугу ар кандай
1. Күнүмдүк өндүрүштө биз көбүнчө контролдоодо кыйынчылыктарга туш болобуз, айрыкча 420дан жогору моделдер үчүн. Мунун себептери болжол менен төмөндөгүдөй жалпыланган:
(1) Гранулдаштыруу үчүн азыктандыруу көлөмү бирдей эмес, жана жумшартуу таасири абдан өзгөрүп турат.
(2) калыптын роликтеринин ортосундагы ыраатсыз ажырым же шакекче көктүн жана басым роликтердин катуу эскириши.
(3) шакек көктүн октук багыты боюнча, эки учундагы разряд ылдамдыгы ортосуна караганда төмөн.
(4) шакек көктүн басым азайтуу тешик өтө чоң, жана ачуу ылдамдыгы өтө жогору.
(5) Кесүүчү бычактын абалы жана бурчу негизсиз.
(6) Грануляция температурасы.
(7) шакек өлүп кесүүчү бычактын түрү жана натыйжалуу бийиктиги (пычак туурасы, туурасы) таасир этет.
(8) Ошол эле учурда компрессиялык камеранын ичиндеги чийки заттардын бөлүштүрүлүшү бирдей эмес.
2. Тоюттун жана гранулдардын сапаты жалпысынан ички жана тышкы сапаттарына жараша талданат. Өндүрүш системасы катары биз тоют гранулдарынын сырткы сапатына байланыштуу нерселерге көбүрөөк дуушар болобуз. Өндүрүштүк көз караштан алганда, суу тоют гранулдарынын сапатына таасир этүүчү факторлор болжол менен төмөнкүчө чагылдырууга болот:
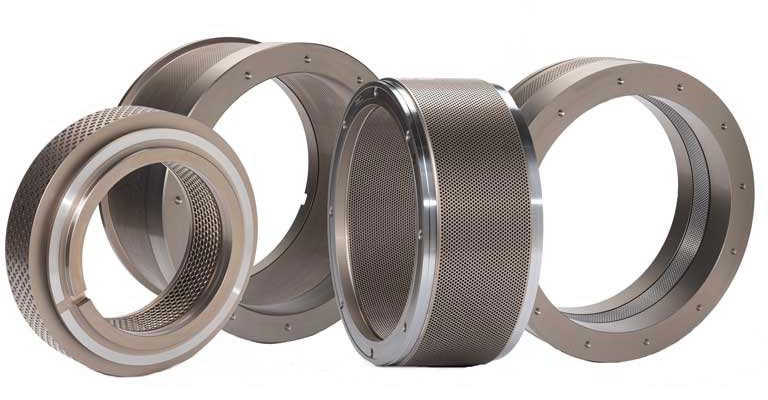
(1) Формулаларды долбоорлоо жана уюштуруу суудагы тоют гранулдарынын сапатына түздөн-түз таасирин тийгизет, жалпы көлөмүнүн болжол менен 40% түзөт;
(2) майдалоонун интенсивдүүлүгү жана бөлүкчөлөрдүн өлчөмүнүн бирдейлиги;
(3) шакекче калыптын диаметри, кысуу катышы жана сызыктуу ылдамдыгы бөлүкчөлөрдүн узундугуна жана диаметрине таасирин тийгизет;
(4) кысуу катышы, сызыктуу ылдамдыгы, шакекче калыптын өчүрүү жана жумшартуу таасири жана бөлүкчөлөрдүн узундугуна кесүүчү бычактын таасири;
(5) чийки заттын нымдуулугу, жумшартуу эффектиси, муздатуу жана кургатуу даяр продукциянын нымдуулугуна жана сырткы көрүнүшүнө таасирин тийгизет;
(6) Жабдыктын өзү, процесс факторлору жана өчүрүү жана чымырлоочу эффекттер бөлүкчөлөрдүн порошок мазмунуна таасирин тийгизет;
3. Иштөө чаралары:
(1) Кездеме кыргычтын узундугун, туурасын жана бурчун тууралаңыз жана эскирген кыргычты алмаштырыңыз.
(2) Аз азыктандыруу көлөмүнө байланыштуу өндүрүштүн башында жана аягында кесүүчү бычактын абалын өз убагында тууралоого көңүл буруңуз.
(3) Өндүрүштүк процесстин жүрүшүндө, туруктуу азыктандыруу ылдамдыгын жана буу менен камсыз кылуу. Эгерде буу басымы төмөн болуп, температура көтөрүлө албаса, аны өз убагында жөнгө салуу же токтотуу керек.
(4) ортосундагы ажырымды жөндөөгөролик кабык. Жаңы калыпты жаңы роликтер менен ээрчип, эскиргендиктен басым роликтин жана шакекче калыптын тегиз эмес бетин тез арада оңдоңуз.
(5) Шакек калыптын жетектөөчү тешигин оңдоп, бөгөлгөн калыптын тешигин тез арада тазалаңыз.
(6) шакек көк заказ жатканда, баштапкы шакек көктүн октук багытынын эки учундагы тешиктердин үч катар кысуу катышы ортосуна караганда 1-2mm кичирээк болушу мүмкүн.
(7) жумшак кесүүчү бычакты колдонуңуз, калыңдыгы 0,5-1мм ортосунда көзөмөлдөнүп, шакекче калып менен басым роликтин ортосундагы торчо сызыкта болушу үчүн, мүмкүн болушунча курч четин камсыз кылуу.
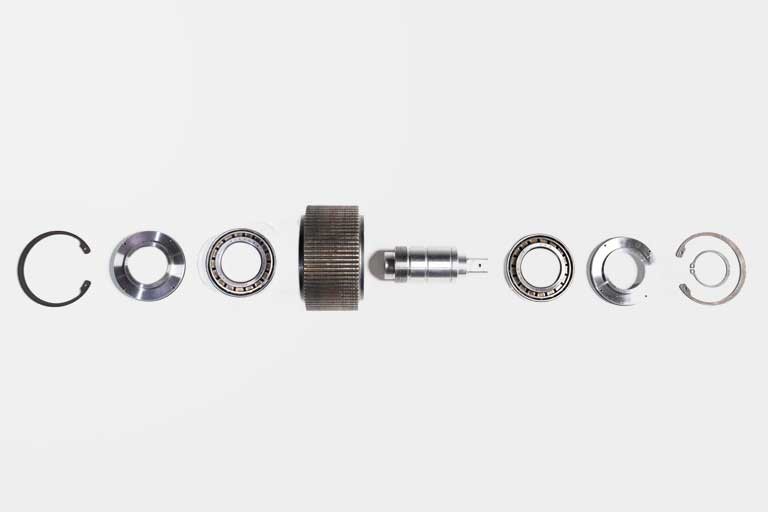
(8) Шакек калыптын концентрдүүлүгүн камсыз кылыңыз, гранулятордун шпиндель клиренсин үзгүлтүксүз текшериңиз жана керек болсо аны тууралаңыз.
6, Кыскача контролдоо пункттары:
1. Майдалоо: майдалоонун майдалыгы спецификациянын талаптарына ылайык көзөмөлдөнүшү керек
2. Аралаштыруу: чийки затты аралаштыруунун бирдейлиги, аралашуунун тиешелүү көлөмүн, аралашуу убактысын, нымдуулугун жана температурасын камсыз кылуу үчүн контролдонууга тийиш.
3. Бышып жетилиши: соргуч машинанын басымы, температурасы жана нымдуулугу көзөмөлдөнүшү керек
Бөлүкчөлөрдүн материалынын өлчөмү жана формасы: кысуу калыптарынын жана кесүүчү бычактын тиешелүү мүнөздөмөлөрү тандалышы керек.
5. Даяр тоюттун суусу: Кургатуу жана муздатуу убактысын жана температурасын камсыз кылуу зарыл.
6. Май чачуу: Май чачуунун так көлөмүн, саптамалардын санын жана майдын сапатын көзөмөлдөө керек.
7. Скрининг: Материалдын спецификациясына ылайык электин өлчөмүн тандаңыз.
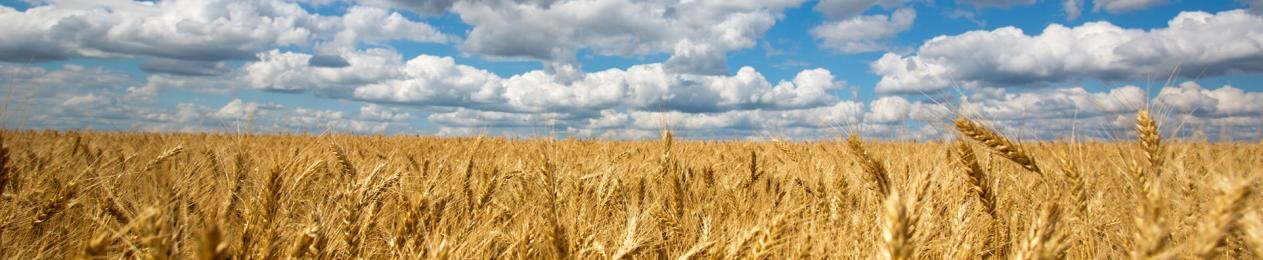
Посттун убактысы: Ноябр-30-2023