Пеллет машинасы - бул биомассаны кысуу үчүн прибор жана гранул тоют, алардын арасында басым ролик анын негизги компоненти жана аялуу бөлүгү болуп саналат. Анын оор жүктөмүнөн жана катаал эмгек шартынан улам, жогорку сапатта болсо дагы, эскирүүгө болбойт. Өндүрүш процессинде басым роликтерин керектөө жогору, ошондуктан басым роликтеринин материалдык жана өндүрүш процесси өзгөчө маанилүү.
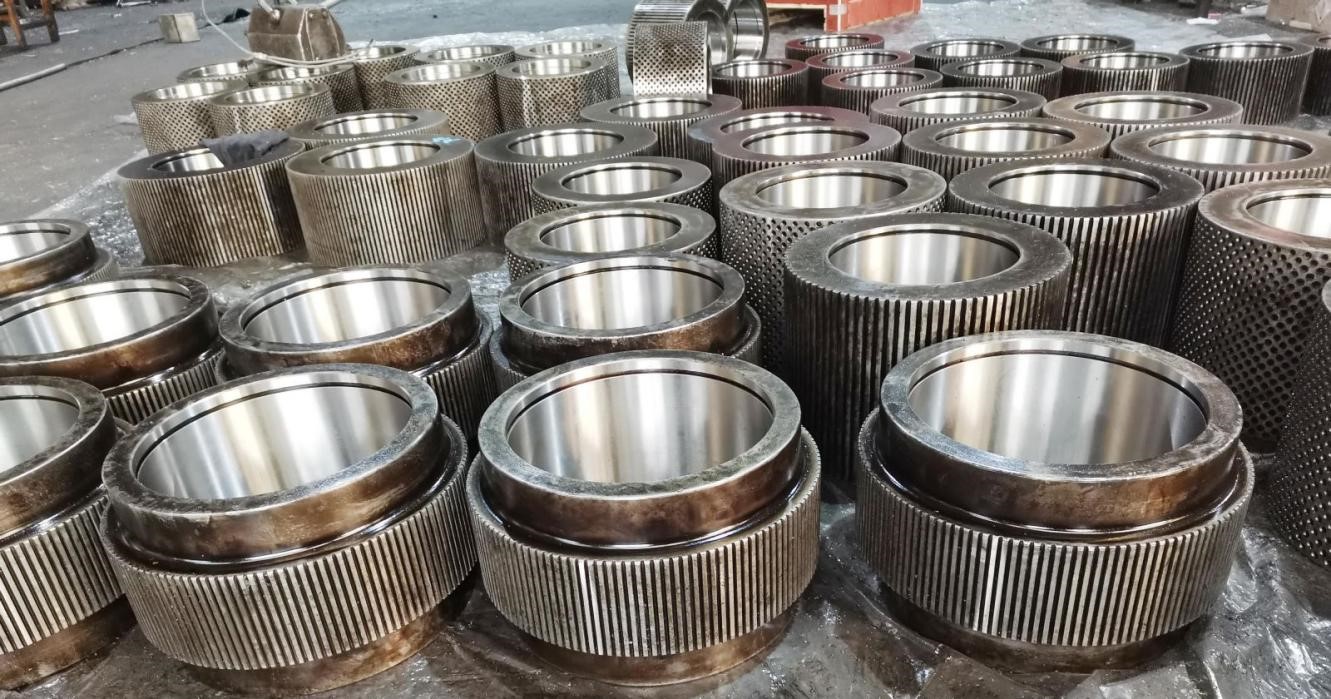
Бөлүкчөлөр машинасынын басым роликинин бузулушунун анализи
Басым роликтин өндүрүш процесси төмөнкүлөрдү камтыйт: кесүү, согуу, нормалдаштыруу (аннеалдоо), орой иштетүү, өчүрүү жана чындоо, жарым тактык иштетүү, беттик өчүрүү жана так иштетүү. Профессионалдуу топ өндүрүш жана кайра иштетүү үчүн биомассалык гранул күйүүчү майлардын эскириши боюнча эксперименталдык изилдөөлөрдү жүргүздү, бул ролик материалдарды жана жылуулук менен иштетүү процесстерин рационалдуу тандоо үчүн теориялык негизди түздү. Төмөндө изилдөөлөрдүн корутундулары жана сунуштары келтирилген:
Гранулятордун басым роликинин бетинде чийик жана чийик пайда болот. Басым роликтеги кум жана темир бөлүкчөлөрү сыяктуу катуу аралашмалардын эскиришине байланыштуу анормалдуу эскирүүгө кирет. Орточо беттик эскирүү болжол менен 3 мм, ал эми эки тараптын эскириши ар башка. Берүү жагы катуу эскириши менен, 4,2 мм. Негизинен тамактандыруудан кийин гомогенизатор материалды бирдей бөлүштүрүүгө үлгүрбөй калгандыктан, экструзия процессине киришкен.
Микроскопиялык эскирүүнүн бузулушунун анализи көрсөткөндөй, чийки зат менен шартталган басым роликтин бетиндеги октук эскирүүлөрдөн, басым роликтин бетиндеги материалдын жоктугу бузулуунун негизги себеби болуп саналат. Негизги эскирүү формалары жабышчаак эскирүү жана абразивдүү эскирүү болуп саналат, морфологиясы катаал чуңкурлар, соко кыркалары, соко оюктары ж. Суу буусунун жана башка факторлордун таасиринен басым роликтин бетинде баткак сымал оймо-чиймелер пайда болуп, басым роликтин бетинде стресстик коррозия жаракалар пайда болот.
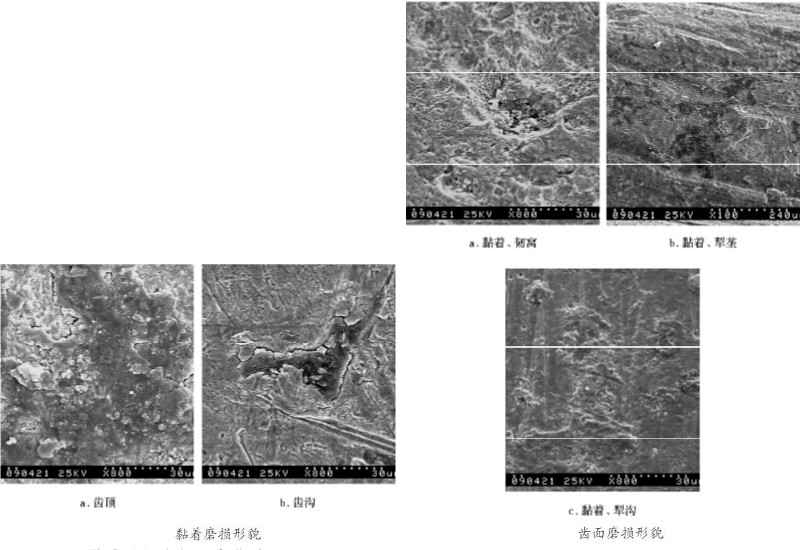
Чийки затты майдалоодон мурун чийки затка аралашкан кум бөлүкчөлөрүн, темир бөлүкчөлөрүн жана башка аралашмаларды алып салуу процессин кошуу сунушталат, бул басым роликтерде анормалдуу эскирүүнү жана эскирүүнү болтурбоо үчүн. Скрепердин формасын же орнотуу абалын өзгөртүп, материалды кысуу камерасында бирдей бөлүштүрүү, басым роликтин тегиз эмес күчүнүн алдын алуу жана басым роликтин бетинин эскиришин күчөтүү. Басым ролик негизинен беттик эскирүүдөн улам иштебей калгандыктан, анын жогорку беттик катуулугун, эскирүү туруктуулугун жана коррозияга туруктуулугун жогорулатуу үчүн, эскирүүгө туруктуу материалдарды жана ылайыктуу жылуулук менен дарылоо процесстерин тандоо керек.
басым роликтер материалдык жана технологиялык дарылоо
Басым роликтин материалдык курамы жана процесси анын эскирүүгө туруктуулугун аныктоо үчүн зарыл шарттар болуп саналат. Көбүнчө колдонулган ролик материалдарына C50, 20CrMnTi жана GCr15 кирет. өндүрүш процесси CNC станок инструменттерин колдонот, жана ролик бети муктаждыктарына жараша түз тиштери, кыйгач тиштери, бургулоо түрлөрү, ж.б. Роликтин деформациясын азайтуу үчүн карбюризацияны өчүрүү же жогорку жыштыктагы өчүрүү жылуулук дарылоо колдонулат. жылуулук менен дарылоо кийин, так иштетүү роликтин кызмат мөөнөтүн узарта алат ички жана тышкы тегеректердин концентрдүүлүгүн камсыз кылуу үчүн кайра жүзөгө ашырылат.
басым роликтер үчүн жылуулук дарылоо мааниси
Басым роликтин иштеши жогорку бекемдиктин, жогорку катуулуктун (кийүүгө туруктуулугу) жана жогорку катуулуктун, ошондой эле жакшы иштетилүүчүлүгүнүн (анын ичинде жакшы жылтылоонун) жана коррозияга туруктуулугунун талаптарына жооп бериши керек. Басым роликтерин жылуулук менен иштетүү - бул материалдардын потенциалын ачууга жана алардын иштешин жакшыртууга багытталган маанилүү процесс. Бул өндүрүштүн тактыгына, күч-кубатына, кызмат мөөнөтүнө жана өндүрүштүк чыгымдарга түздөн-түз таасирин тийгизет.
Ошол эле материал үчүн, ашыкча ысытуудан өткөн материалдар ашыкча ысып кетүүдөн өтпөгөн материалдарга салыштырмалуу бир топ жогору күчкө, катуулугуна жана бекемдигине ээ. Эгерде өчүрүлбөсө, басым роликтин иштөө мөөнөтү бир топ кыска болот.
Эгер сиз так иштетүүдөн өткөн термикалык иштетилген жана термикалык иштетилбеген тетиктерди айырмалоону кааласаңыз, аларды катуулугу жана термикалык иштетилген кычкылдануу түсү боюнча гана айырмалоо мүмкүн эмес. Эгер сиз кесип жана сынагыңыз келбесе, анда үндү басуу менен аларды айырмалоого аракет кылсаңыз болот. Металлографиялык түзүлүшү жана куймалардын жана өчүрүлгөн жана чыңдалган дайындамалардын ички сүрүлүүсү ар түрдүү, аларды жумшак таптатуу менен айырмалоого болот.
Жылуулук менен дарылоонун катуулугу бир нече факторлор менен аныкталат, анын ичинде материалдын классы, өлчөмү, даярдалган бөлүгүнүн салмагы, формасы жана түзүлүшү жана андан кийинки иштетүү ыкмалары. Мисалы, чоң тетиктерди жасоо үчүн пружиналык зымды колдонууда, даярдалган бөлүктүн чыныгы калыңдыгына байланыштуу, колдонмодо термикалык иштетүүнүн катуулугу 58-60HRC жетиши мүмкүн, аны иш жүзүндөгү даярдалган тетиктер менен айкалыштырууга мүмкүн эмес деп айтылат. Мындан тышкары, өтө жогорку катуулук сыяктуу негизсиз катуулук индикаторлору даярдалган тетиктин катуулугун жоготууга алып келиши мүмкүн жана колдонуу учурунда жаракаларды жаратышы мүмкүн.
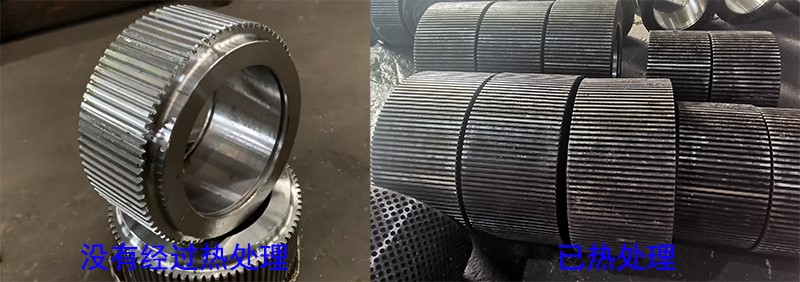
Жылуулук менен дарылоо квалификациялуу катуулук маанисин гана камсыз кылбастан, анын процессин тандоого жана процессти көзөмөлдөөгө да көңүл буруу керек. Ашыкча ысып кеткен өчүрүү жана жумшартуу талап кылынган катуулукка жете алат; Ошо сыяктуу эле, өчүрүү учурунда ысытууда, чыңдоо температурасын жөнгө салуу да талап кылынган катуулуктун диапазонуна жооп бере алат.
Baoke басым ролик булактан бөлүкчө машина басым роликтин катуулугун жана эскирүү туруктуулугун камсыз кылуу, жогорку сапаттагы болот C50 жасалган. Жогорку температурадагы өчүрүүчү жылуулук менен дарылоонун эң сонун технологиясы менен айкалышып, анын кызмат мөөнөтүн кыйла узартат.
Посттун убактысы: Jun-17-2024